Enhancing Performance and Quality Via Modern Metal Stamping Techniques
As the demands for precision and effectiveness proceed to rise, the assimilation of automation and digital tools into the metal marking procedure has actually become critical. By exploring the intricate interplay in between modern technology, automation, and accuracy in metal stamping, a pathway towards exceptional efficiency and quality assurance unravels.
Advantages of Modern Metal Stamping
Modern steel stamping offers numerous benefits in regards to effectiveness, precision, and cost-effectiveness in the production market. One of the key benefits of contemporary metal marking is its capability to efficiently generate high quantities of complex steel get rid of consistent top quality. This procedure eliminates the need for several operations as it can perform different tasks such as blanking, puncturing, developing, and attracting in a solitary operation.
In addition, contemporary steel marking enables suppliers to accomplish tight resistances and precise requirements, making certain that each part fulfills the needed standards. This high level of accuracy leads to marginal material waste, lowered rework, and general improved product top quality.
In addition, modern-day metal stamping is an economical production approach. In significance, modern metal stamping offers an affordable side to producers looking to improve efficiency and top quality in their procedures.
Advanced Technologies in Steel Stamping
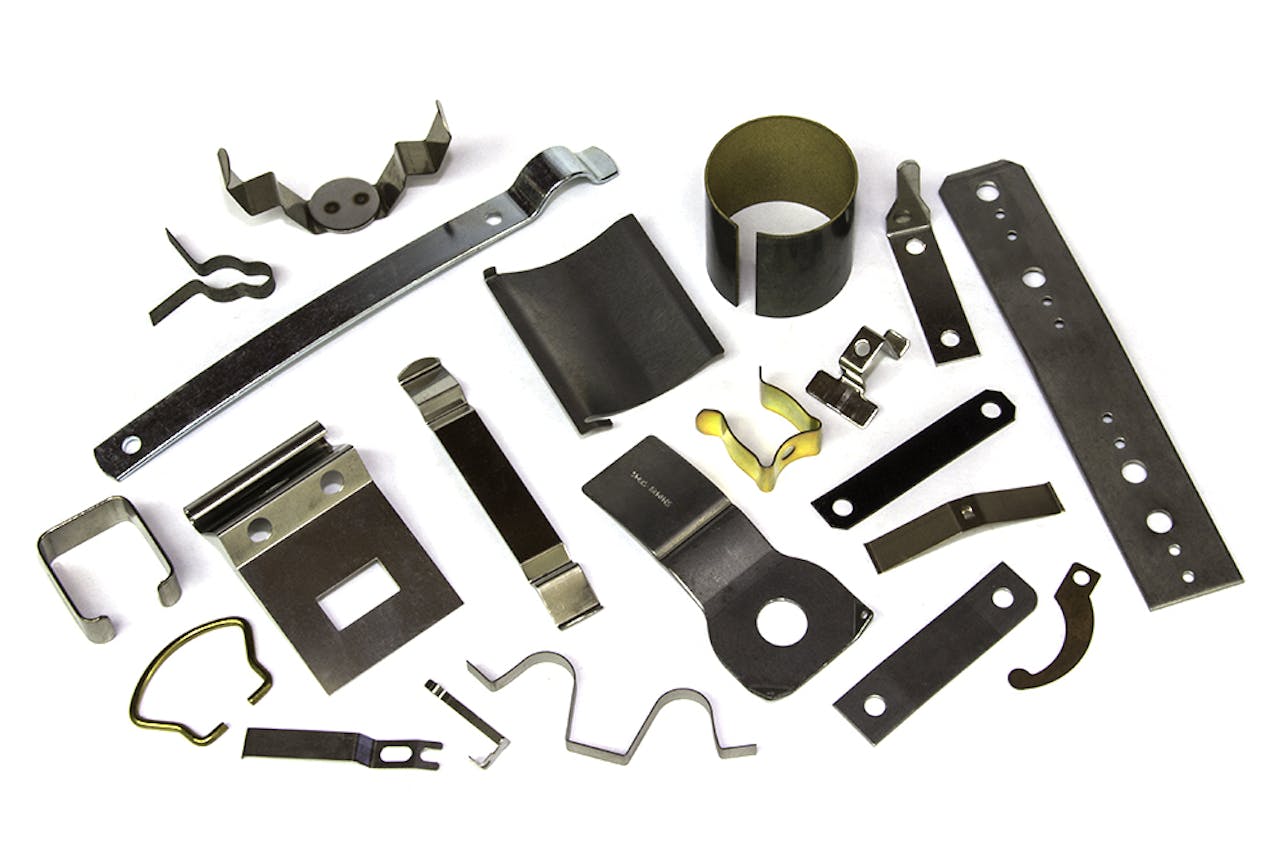
An additional vital innovation reinventing metal marking is making use of servo presses. Unlike standard mechanical presses, servo presses provide greater control over the rate and pressure applied throughout the stamping process. This control not just improves the quality of the stamped components however also lowers product waste and energy intake.
In addition, improvements in simulation software have actually allowed manufacturers to virtually check and optimize the marking process prior to physical production starts. This online prototyping helps recognize prospective concerns early, leading to set you back savings and faster time-to-market for new items. In general, these innovative innovations in steel stamping are driving extraordinary levels of efficiency and quality in the market.
Improving Performance Through Automation
The assimilation of automated systems has substantially boosted the efficiency of steel marking processes. Automation in steel marking operations provides a myriad of advantages, including boosted manufacturing rates, enhanced precision, and reduced labor expenses. By utilizing robot arms and computer-controlled machinery, tasks that were previously lengthy and vulnerable to errors can now be carried out promptly and with remarkable precision.
Automated systems have the ability to take care of repetitive tasks with consistency, leading to greater performance degrees and reduced cycle times. This enhanced effectiveness not just brings about set you back savings but also guarantees a much more structured and trusted manufacturing procedure. Additionally, automation permits real-time monitoring and data collection, enabling producers to determine and deal with problems immediately, additional enhancing the general effectiveness of metal stamping operations.
Moreover, automation promotes a safer working setting by lowering the demand for hand-operated treatment in harmful tasks. By entrusting these responsibilities to automated systems, workers can focus on even more complicated and value-added activities, contributing to a more reliable and effective process in the metal stamping sector.
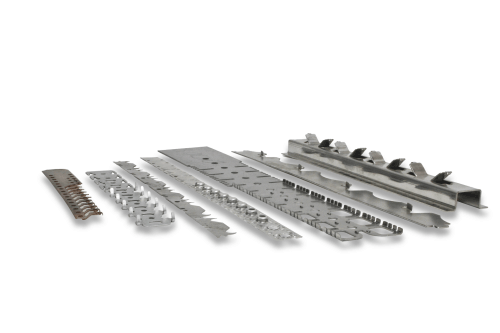
Quality Assurance Procedures in Stamping
Executing stringent top quality control procedures is vital in guaranteeing the precision and uniformity of metal stamping procedures. By establishing durable high quality control procedures, my website manufacturers can recognize and remedy any inconsistencies or flaws in the stamped parts, inevitably improving product top quality and customer satisfaction. Among the primary top quality control steps in steel stamping is performing routine inspections throughout the manufacturing cycle. These evaluations entail checking the measurements, surface coating, and overall stability of the stamped components to confirm compliance with the given needs.
Furthermore, implementing sophisticated modern technologies such as automated vision systems can further enhance the quality assurance process by allowing real-time tracking and discovery of any anomalies throughout manufacturing. These systems make use of video cameras and computer formulas to evaluate get rid of high precision and accuracy, lessening the threat of defects leaving into the last item.
Furthermore, establishing a comprehensive documentation system that records quality control data and inspection outcomes is crucial for tracking efficiency fads and assisting in constant enhancement efforts. By evaluating this data, manufacturers can recognize possible areas for optimization and execute corrective activities to boost the general quality of their stamped products.
Enhancing Accuracy With Digital Equipment
Employing electronic devices can substantially enhance the accuracy of steel stamping procedures, changing the method manufacturers attain precision in their production. Digital devices such as computer-aided style (CAD) software permit for the development of elaborate marking styles with incredibly specific measurements. By inputting detailed requirements into the software program, makers can ensure that each stamped item meets specific dimensional requirements, lowering errors and waste in the manufacturing process.
In addition, Recommended Site the combination of sensing units and real-time tracking systems in marking equipment makes it possible for producers to very closely keep track of the marking process and make instant changes to guarantee specific results. These electronic devices offer beneficial data on variables such as pressure, rate, and positioning, permitting quick identification and improvement of any variances from the desired specs.
Verdict
To conclude, contemporary steel marking methods provide countless advantages for enhancing efficiency and top quality in manufacturing processes. By using sophisticated modern technologies, automation, read the article quality assurance steps, and digital devices, firms can boost efficiency, precision, and general performance. These advancements in steel marking not just streamline production processes but likewise guarantee constant and high-grade outcomes. Welcoming these modern techniques can lead to significant developments in the manufacturing industry.